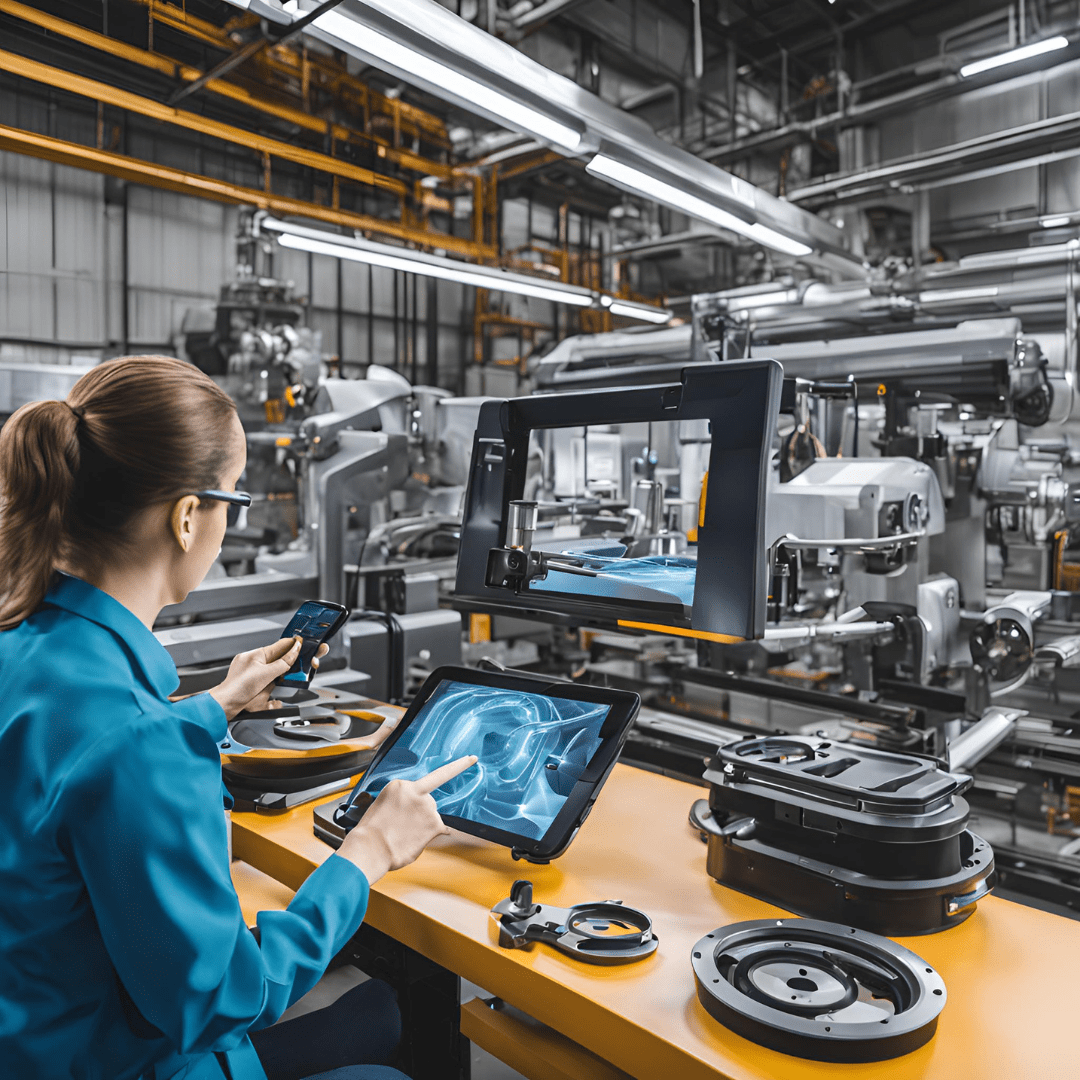
Introduction
In the fast-changing environment of technology, AR has been one of the game-changing inventions or innovations, especially for the manufacturing industry. AR offers leading-edge ability in productivity, accuracy, and safety through digital display of information on top of real-world settings. This blog explores how AR is going to revolutionize manufacturing, its major applications, advantages, and trends that would be followed in the future.
Understanding Augmented Reality in Manufacturing
Augmented reality merges digital content to blend into the real world, interactively experienced through such devices as smartphones, tablets, and AR glasses. This roughly corresponds, in manufacturing, to overlaying technical information, instructions, and data onto machinery, parts, and production lines.
Key Applications of AR in Manufacturing
1. Assembly and Production
AR can guide workers through complex assembly processes, as it projects step-by-step instructions directly onto the components. This reduces errors and speeds up production times.
2. Maintenance and Repair
In this regard, AR can be utilized in identifying issues and providing real-time repair guidance, therefore reducing downtimes and improving efficiency. Parts that require attention could be highlighted, and graphical instructions provided in an AR display.
3. Quality Control
AR enhances the quality control process by allowing inspectors to compare products against 3D models. Any discrepancies become highly visible, attaining better standards and reducing waste.
4. Training and Skill Development
AR makes the process of training new employees much easier. Interactive simulations provide hands-on experience without the risk of damaging equipment. This leads to faster learning curves and better retention.
5. Design and Prototyping
AR enables engineers and designers to visualize and manipulate 3D models of products within the real environment. This facilitates spotting design flaws at an early stage and simplifies the phase of prototyping.
Benefits of AR in Manufacturing
1. Enhanced Productivity
AR provides real-time information and guidance, reducing time usage for many different tasks, increasing overall productivity.
2. Improved Accuracy
AR reduces human error by giving relevant instructions and feedback in real time. This proves very important in any industry that requires precision.
3. Cost Reduction
On the bottom line, reduced errors, faster training, and reduced downtime mean huge savings. AR helps in the optimization of resource usage, hence bringing down operational costs.
4. Increased Safety
AR could then identify safety risks and guide workers through safe practices, thus avoiding accidents on the factory floor.
5. Better Collaboration
AR allows remote collaboration in such a way that expertise can be provided and guidance can be given to on-site personnel in real-time from anywhere in the world. This becomes particularly useful for those multinational firms with dispersed employees.
Case Studies: AR in Action
1. Boeing
Boeing has integrated AR into their production lines. With AR glasses, technicians see complex wiring diagrams right on the aircraft components. This has drastically quickened production time while reducing resultant errors correspondingly.
2. BMW
BMW uses AR for maintenance and repair. AR glasses help technicians by illustrating steps and highlighting components, which controls the difficulty of complicated repairs.
3. GE Renewable Energy
AR is used for wind turbine maintenance at GE Renewable Energy. Here, technicians using AR get real-time data and instructions in the process of maintenance, therefore improving efficiency and safety. Also, check Data Analysis.
Challenges and Considerations
1. Implementation Costs
The initial investment in AR technology can be substantial. Companies need to consider the cost of hardware, software, and training.
2. Integration with Existing Systems
Seamless integration of AR with existing manufacturing systems can be challenging. It requires robust IT infrastructure and skilled personnel.
3. Data Security
With AR relying heavily on data, ensuring data security and protecting intellectual property is crucial.
4. Workforce Adaptation
Employees need to be adequately trained to use AR technology effectively. Resistance to change can be a barrier to successful implementation.
Future Trends of AR in Manufacturing
1. Enhanced Wearable Devices
Future AR devices will be more ergonomic and user-friendly, making them more practical for long-term use in manufacturing environments.
2. AI Integration
Combining AR with artificial intelligence will enable smarter, more predictive AR applications, further enhancing efficiency and accuracy.
3. Increased Adoption of 5G
The rollout of 5G networks will provide the necessary bandwidth and low latency for more advanced AR applications, facilitating real-time data exchange and collaboration.
4. Expanded Applications
AR will find new applications in areas like supply chain management, logistics, and customer support, further transforming the manufacturing sector.
Conclusion
Augmented reality can literally transform the manufacturing sector for good in productivity, accuracy, and safety. With rapidly advancing technology, AR applications and benefits will only grow for improving efficiency in industry operations. It is obvious that adopting AR now implies a much more competitive and technologically advanced future for manufacturers.
How does AR improve manufacturing processes?
AR enhances manufacturing by providing real-time information and instructions, reducing errors, speeding up production, and improving safety.
What are the main benefits of AR in manufacturing?
The main benefits include increased productivity, improved accuracy, cost reduction, enhanced safety, and better collaboration.
What are some challenges of implementing AR in manufacturing?
Challenges include high implementation costs, integration with existing systems, data security concerns, and workforce adaptation.
Can AR be used for training in manufacturing?
Yes, AR is highly effective for training, offering interactive simulations that help new employees learn quickly and efficiently.
What are future trends of AR in manufacturing?
Future trends include enhanced wearable devices, AI integration, increased 5G adoption, and expanded applications across various aspects of manufacturing.
How is AR used in quality control?
AR is used in quality control by allowing inspectors to compare products against 3D models, highlighting discrepancies for immediate correction.
Explore More :